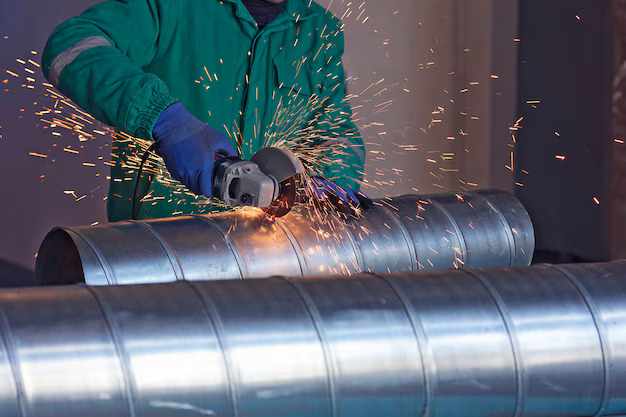
Low-cost, versatile, and durable materials are precious in the current industrial and construction industries. One of these materials that has revolutionized most applications across the two industries is galvanized iron (GI) coils. These sheets of metal work efficiently across different environments and uses since they are produced by protecting steel or iron with the zinc coating. Experts in the sector should be informed of the benefits of GI coils because of the increasing demand for reliable materials. In this blog, we will explore seven most significant benefits that make GI coils an integral part of contemporary production and building.
What are GI coils?
Hot Dip Galvanized Steel Coil is manufactured by immersing cold-rolled steel in a molten bath of zinc at temperatures of approximately 460 degrees Celsius. The zinc coating over the steel coil substrate serves as a barrier between the atmosphere and the metal surface. In other words, it is produced by cold-rolled steel sheets dipped in a molten zinc bath at elevated temperatures. The zinc coating forms a protective barrier against moisture and corrosive substances for the steel.
What are GI coils used for?
Construction: GI coils are applied to roofing, siding, gutters, and decking.
Automotive: GI coils are used in vehicle panels, chassis components, and other applications.
Appliances: GI coils are employed in refrigerators, washing machines, and other appliances.
General engineering: GI coils work in various applications, like the production of doors and roofs.
7 Key Advantages of Using GI Coils in Construction and Manufacturing
1. Superior Corrosion Resistance
The key benefit of GI coils is that they are extremely corrosion-resistant. The galvanization process deposits a protective zinc coat over the iron substrate, which forms a barrier that protects the base metal from atmospheric conditions. The zinc coat acts on two levels: first, as a physical coating, which stops oxygen and moisture from touching the steel, and secondly, as a sacrificial anode, where the zinc gets corroded first to preserve the underlying metal.
Even after the coating has been scratched or broken, surrounding zinc continues to shield the exposed steel through cathodic protection. This incredible property enables GI coils to endure hard conditions such as humid conditions, coastal environments, and industrial atmospheres where the presence of corrosive agents is prevalent. The outcome is a much longer service life in comparison to unprotected steel, hence GI coils being very useful for outdoor applications.
2. Cost-Effectiveness
Although the upfront cost of GI coils can be more than uncoated options, their long-term financial advantages easily offset this initial expenditure. The longer life of galvanized products equates to considerable savings through:
Lower maintenance expenses: GI coils need little maintenance, obviating the need for periodic painting or rusting treatments
Less replacement: With service lives commonly in excess of 50 years in most applications, replacement frequency is substantially less
Reduced installation costs: GI coils' strength results in reduced disruptions and reinstallation costs down the road
Less downtime: Products and buildings utilizing GI coils are less prone to failures and resulting operation downtime
If one calculates the overall cost throughout the lifetime of the application, GI coils consistently rank among the most cost-effective solutions possible. This value translates into significant advantages for bulk construction projects in which material cost makes up a major percentage of total expenditures.
3. Versatility and Wide Range of Applications
The amazing flexibility of GI coils has established them as widely used materials in various applications in construction and manufacturing industries alike. These adaptable materials can be identified in:
Construction Applications:
Roofing and cladding systems
HVAC ducting and ventilation parts
Structural frames
Gutters and drainage systems
Freeway guardrails and safety barriers
Manufacturing Applications:
Household appliances (washing machines, fridges)
Vehicle components
Electrical enclosures and equipment cases
Storage tanks and containers
Farm equipment
This flexibility is due to the fact that GI coils can be shaped, cut, welded, and joined with regular metalworking methods. They also accept an array of finishes, such as paints and powder coatings, that further increase their possibility of use. There are few materials that can compete with the flexibility of GI coils in so many different applications.
4. Durability and Strength
GI coils unite the inherent toughness of steel with the protective benefits of zinc, yielding a product that outperforms in extreme applications. The galvanizing process actually strengthens the mechanical properties of the underlying metal in numerous ways:
The harder zinc-iron alloy layers developed in galvanizing are harder than the substrate steel, enhancing abrasion resistance
The coating process removes internal stresses within the steel, minimizing distortion potential
The zinc coating offers impact resistance, which guards against physical damage
This added strength is reflected in excellent performance in demanding conditions. GI coils retain their structural integrity in cold temperatures, accept heavy loads, and resist impairment from vibration and movement. In uses where reliability is paramount, like structural members or areas of heavy traffic, the strength of GI coils renders them the perfect solution.
5. Ease of Processing and Fabrication
Though possessing great strength, GI coils are still very workable and easy to process through conventional metalworking methods. Producers and fabricators value the following key features:
High formability, enabling intricate shapes and profiles
Versatility in different joining techniques, such as welding, riveting, and mechanical fastening
Good machinability for cutting, drilling, and punching operations
Consistent behavior during processing, reducing waste and rework
Contemporary GI coils come in a variety of thicknesses and weights of zinc coating, enabling fabricators to choose the best specifications for their specific application needs. This versatility, along with widely proven processing methods, makes GI coils one of the most fabricator-friendly products available in the market.
Environmental Benefits
Though possessing great strength, GI coils are still very workable and easy to process through conventional metalworking methods. Producers and fabricators value the following key features:
High formability, enabling intricate shapes and profiles
Versatility in different joining techniques, such as welding, riveting, and mechanical fastening
Good machinability for cutting, drilling, and punching operations
Consistent behaviour during processing, reducing waste and rework
Contemporary GI coils come in a variety of thicknesses and weights of zinc coating, enabling fabricators to choose the best specifications for their specific application needs. This versatility, along with widely proven processing methods, makes GI coils one of the most fabricator-friendly products available in the market.
Aesthetic Appeal and Finish Options
In addition to their utilitarian advantages, GI coils provide aesthetic flexibility that architects and designers enjoy. The default spangle (crystallized pattern) of newly galvanized steel possesses its own industrial appeal, but GI coils also make a great substrate for other finishes:
The zinc coating is a great substrate for paints and powder coatings
Pre-painted GI coils come in almost any colour
Textured finishes may be applied for speciality looks
The material can be shaped into intricate geometric designs for architectural details
This union of durability and design versatility has led GI coils to become favourites in applications where performance and appearance are both crucial. From clean modern structures to industrial machinery, GI coils offer the ideal balance of function and aesthetics.
Conclusion:
The seven advantages described above—corrosion resistance, cost-effectiveness, versatility, durability, ease of fabrication, environmental benefits, and aesthetic appeal—show why GI coils have become indispensable materials in construction and manufacturing. As industries continue to require materials that provide long-term performance without compromising on costs, the use of GI coils is bound to increase even more. This growing demand has also led to the rise of steel suppliers in UAE, ensuring a steady supply of high-quality GI coils for various applications.
Advances in technology keep refining the characteristics of GI coils, with improvements in coating material, application processes, and raw material formulations. These advances have the potential to extend the already impressive range of uses of these flexible materials, unlocking new uses and enhancing performance in current ones.
Write a comment ...